Porosity in Welding: Identifying Common Issues and Implementing Ideal Practices for Avoidance
Porosity in welding is a pervasive concern that often goes unnoticed till it triggers substantial troubles with the integrity of welds. This usual issue can compromise the stamina and toughness of bonded frameworks, posturing security dangers and bring about expensive rework. By comprehending the origin of porosity and implementing efficient avoidance approaches, welders can significantly improve the high quality and dependability of their welds. In this discussion, we will discover the key elements adding to porosity formation, analyze its destructive impacts on weld performance, and discuss the most effective techniques that can be taken on to reduce porosity event in welding processes.
Usual Causes of Porosity
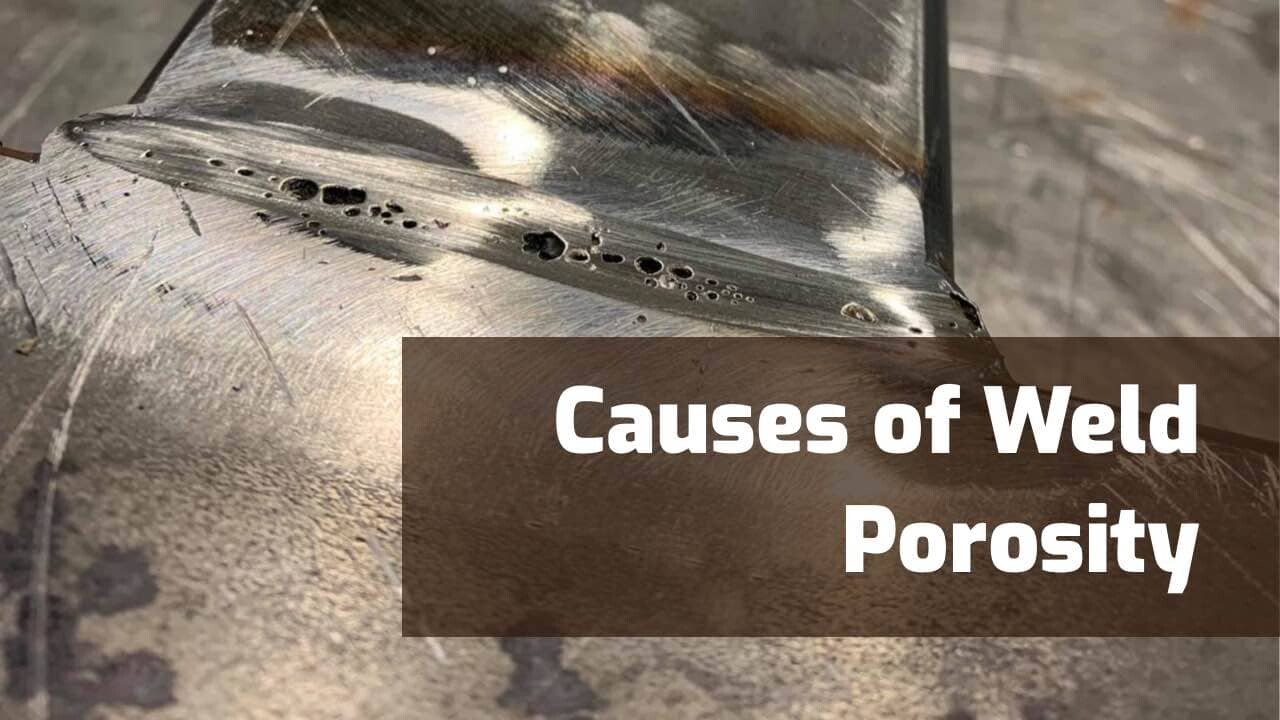
Another frequent offender behind porosity is the visibility of pollutants on the surface area of the base metal, such as oil, grease, or rust. When these impurities are not efficiently gotten rid of prior to welding, they can evaporate and become trapped in the weld, causing defects. Utilizing dirty or wet filler materials can present contaminations right into the weld, adding to porosity concerns. To reduce these usual root causes of porosity, thorough cleansing of base steels, proper protecting gas choice, and adherence to ideal welding specifications are necessary methods in achieving high-grade, porosity-free welds.
Influence of Porosity on Weld Top Quality

The visibility of porosity in welding can significantly jeopardize the structural stability and mechanical residential or commercial properties of bonded joints. Porosity develops gaps within the weld metal, damaging its general toughness and load-bearing capability.
Among the main consequences of porosity is a decrease in the weld's ductility and sturdiness. Welds with high porosity degrees tend to display lower impact stamina and lowered capability to deform plastically prior to fracturing. This can be especially concerning in applications where the welded elements go through vibrant or cyclic loading problems. Furthermore, porosity can hamper the weld's capability to efficiently send forces, bring about early weld failing and potential safety hazards in critical frameworks.
Finest Practices for Porosity Prevention
To boost the structural stability and quality of welded joints, what particular actions can be carried out to reduce the incident of porosity during the welding process? Porosity prevention in welding is crucial to ensure the integrity and strength of the last weld. One efficient practice is correct cleansing of the base steel, her explanation eliminating any type of contaminants such as rust, oil, paint, or dampness that might lead to gas entrapment. Guaranteeing that the welding equipment is in good problem, with clean consumables and suitable gas flow rates, can also substantially minimize porosity. Additionally, preserving a steady arc and regulating the welding specifications, such as voltage, existing, and travel speed, aids develop a regular weld swimming pool that reduces the danger of gas entrapment. Using the appropriate welding strategy for the particular material being bonded, such as adjusting the welding angle and weapon placement, can additionally prevent porosity. Normal evaluation of welds and prompt removal of any concerns identified throughout the welding process are essential methods to avoid porosity and create high-quality welds.
Relevance of Proper Welding Strategies
Applying appropriate welding strategies is vital in ensuring the structural honesty and high quality of welded joints, building upon the foundation of effective porosity prevention steps. Welding techniques straight affect the overall stamina and durability of the bonded framework. One essential aspect of correct welding strategies is preserving the proper warm input. Too much heat can bring about boosted porosity because of the entrapment of gases in the weld swimming read what he said pool. Conversely, insufficient heat may cause incomplete blend, creating prospective weak points in the joint. In addition, making use of the proper welding parameters, such as voltage, current, and travel speed, is vital for achieving audio welds with marginal porosity.
Furthermore, the selection of welding procedure, whether it be MIG, TIG, or stick welding, should line up with the specific demands of the project to make sure optimum results. Correct cleansing and prep work of the base metal, in addition to selecting the appropriate filler material, are likewise necessary elements of efficient welding methods. By sticking to these finest practices, welders can decrease the risk of porosity development and generate high-grade, structurally sound welds.
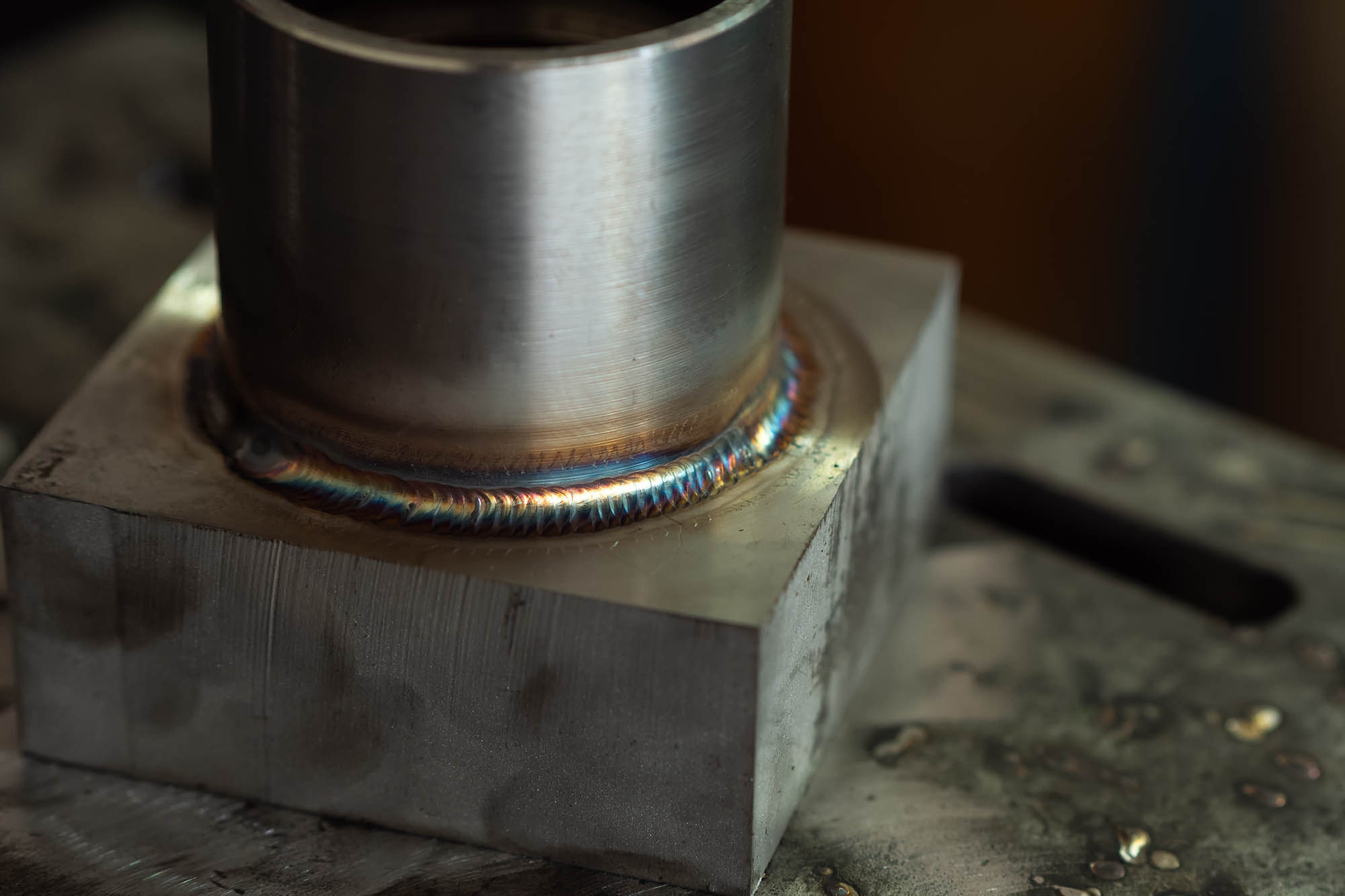
Examining and Quality Assurance Steps
Testing procedures are necessary to spot and avoid porosity in welding, ensuring the strength and durability of the final product. Non-destructive testing approaches such as ultrasonic testing, radiographic testing, and aesthetic evaluation are frequently utilized to recognize potential flaws like porosity.
Performing pre-weld and post-weld evaluations is also essential in preserving high quality control standards. Pre-weld examinations involve validating the materials, devices settings, and cleanliness of the workspace to prevent contamination. Post-weld examinations, on the various other hand, evaluate the last weld for any issues, including porosity, and confirm that it fulfills defined standards. Applying a detailed quality control strategy that consists of extensive screening procedures and examinations is vital to click this reducing porosity concerns and making certain the general top quality of welded joints.
Verdict
In conclusion, porosity in welding can be a typical problem that affects the quality of welds. By determining the typical sources of porosity and executing ideal methods for avoidance, such as proper welding strategies and screening actions, welders can guarantee premium quality and reputable welds. It is necessary to prioritize prevention approaches to reduce the occurrence of porosity and maintain the integrity of welded frameworks.